Image Credit: Joseph Chua
31 August 2021
As firms get carbon conscious, many are opting for mass engineered timber where circumstances suit, says RSP Associate Director Koh Mei Shan
- MET is an increasingly attractive choice of building material – both aesthetically and environmentally.
- The wood is harvested from sustainably-managed forests and helps slash a building’s embodied carbon levels.
- Architects should be mindful of additional design requirements and the longer coordination time.
Imagine working or living in an inviting wood building, surrounded by the fragrant scent, soft hue and warm touch of timber – with the reassurance that it is eco-friendly.
Such Mass Engineered Timber (MET) buildings were few in 2016 when Singapore’s Building and Construction Authority first rolled out its Construction Productivity Roadmap, whose productive technology adoption strategies included the use of MET in DfMA.
These days, there are far more MET projects as developers grow aware of the environmental benefits in achieving a built environment that’s net zero carbon. Notable examples are The Wave, NTU’s mega sports hall, and the NTU Academic Building South.
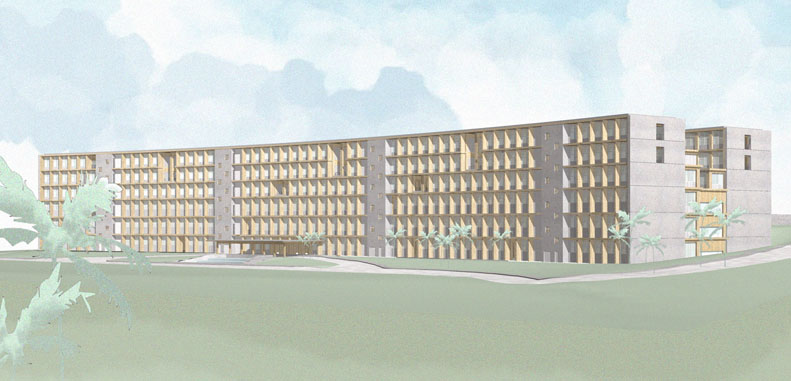
Image Credit: Toyo Ito & Associates, Architects
Sustainably-harvested
MET, which can be used for walls, floors, roofs, columns, beams and truss elements, is made by stacking and bonding layers of renewable timber for improved structural integrity. The certified wood is harvested from sustainably-managed forests.
Such timber requires less energy to manufacture than concrete and steel, helping to slash a development’s embodied carbon levels. While MET projects cost more in the short term as local suppliers are not available, using MET also minimises finishes, reduces construction cost and increases productivity.
Another key benefit is that components are pre-fabricated, which translates to high dimension accuracy and quality control, and less dust and noise, wet works, on-site fabrication, and installation time.
Careful design planning
However, architects should be mindful of additional design requirements and the longer coordination time for MET projects. Detailed strategies to protect the timber’s durability, such as waterproofing and watertightness, should be considered in the early design stages. During construction, modifications should be avoided or minimised to prevent cutting or patching of MET penetrations on-site, as this could jeopardise the wood’s structural integrity and durability.
Since MET is pre-fabricated, elements need to be accurately coordinated with mechanical and electrical services and architectural elements. And if the building exceeds 12 metres in habitable height, a fire safety performance-based design approach needs to be adopted, which typically involves a longer time for building plan application and approval.
It’s important to bear in mind that the best outcomes arise from applying MET in appropriate contexts; as a lightweight, prefabricated material, it’s particularly suitable for small scale modular buildings.
As the world grows more eco-conscious and the need to protect our environment rings more urgent each day. MET is an increasingly attractive choice of building material – both aesthetically and environmentally. It brings nature into building designs, creates a welcoming, comforting environment, and is good for users in more ways than one.
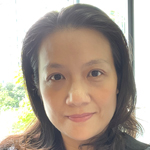
Koh Mei Shan, Associate Director, Singapore Studio
Koh Mei Shan has more than 17 years of architectural experience, working on a diverse range of projects including residential, offices, retail and education projects. Her major projects in Singapore include NTU Academic Building South, NTU Pioneer & Crescent Halls, Woh Hup Building and Temasek Polytechnic upgrading projects. Overseas, she was part of the architectural team in the earlier conception for the mixed development project at Palm Jumeirah and Rihan Heights residential project in United Arab Emirates.
Share